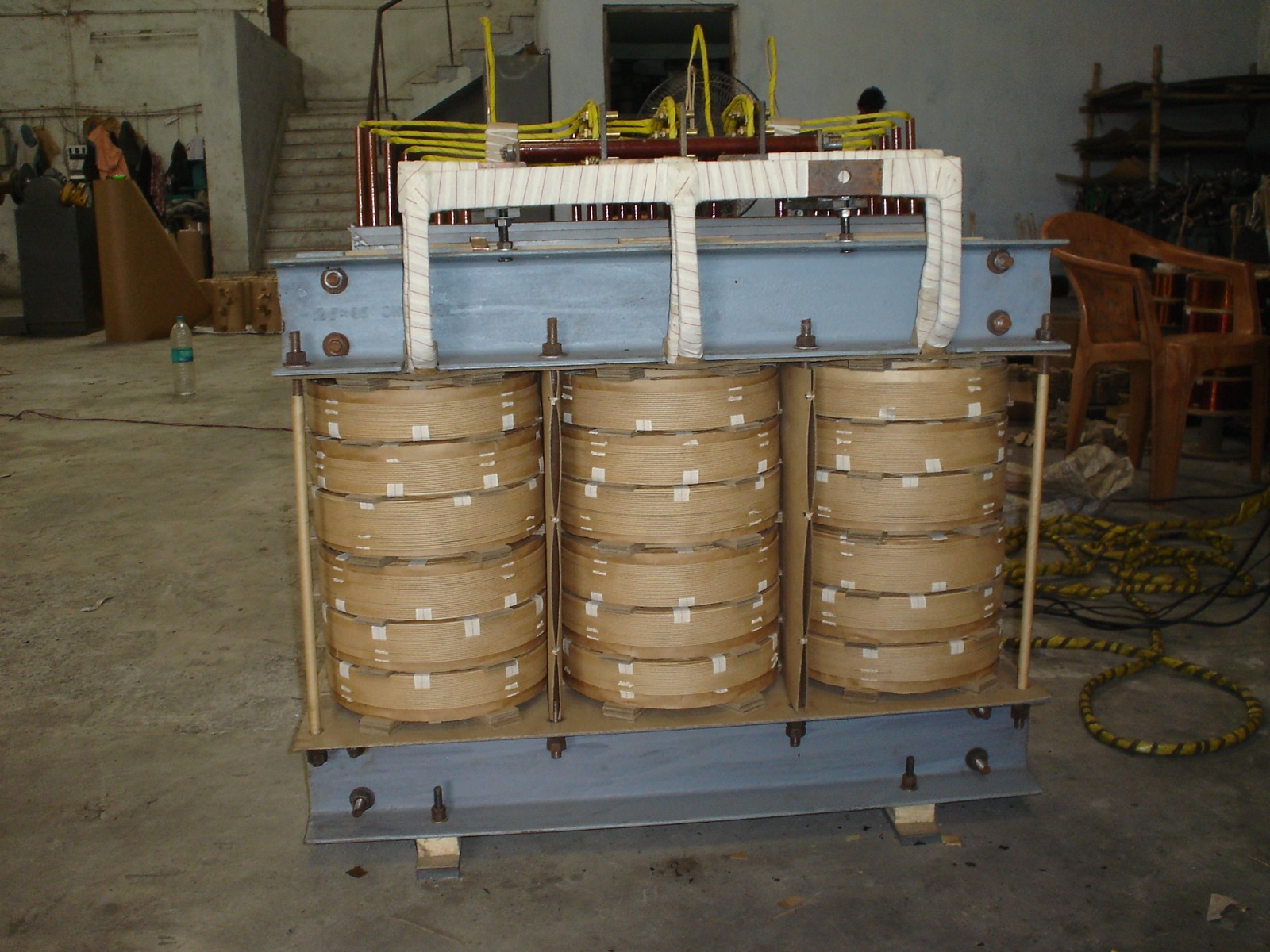
COIL WINDING
The coil winding process is a critical phase in transformer manufacturing that significantly impacts the transformer's performance, efficiency, and longevity. The process begins with careful preparation, where high-quality copper or aluminum wires are selected for their excellent conductivity and mechanical strength. High-grade insulating materials such as paper, varnish, or enamel are also chosen to ensure electrical isolation between turns and layers. Design specifications are meticulously calculated, inc
CORE ASSEMBLY
One of The main items of Transformer is Core or Lamination(COLD ROLLED GRAIN ORIENTED-C.R.G.O) Silicon steel. CRGO of required thickness, shall be used, to obtain the desired losses, confirming to IS: 649 of 1983 & IS:3024-1965. The core shall be cut as per design and annealing is done thereafter. These laminations are assembled in such a way that there is no air gap between the joints of two consecutive sheets. The entire assembly is done on a frame commonly known as core channel, used as clampin
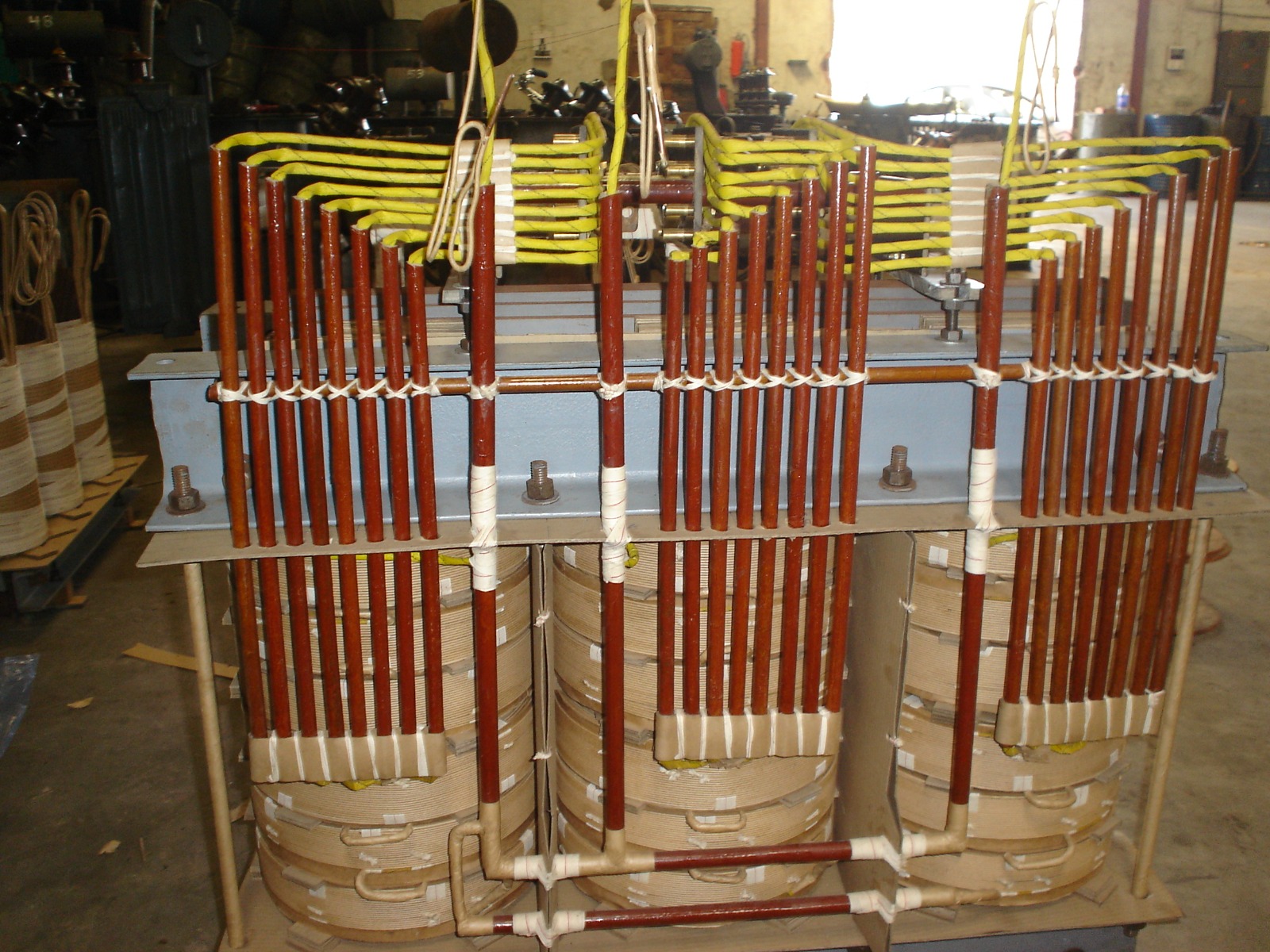
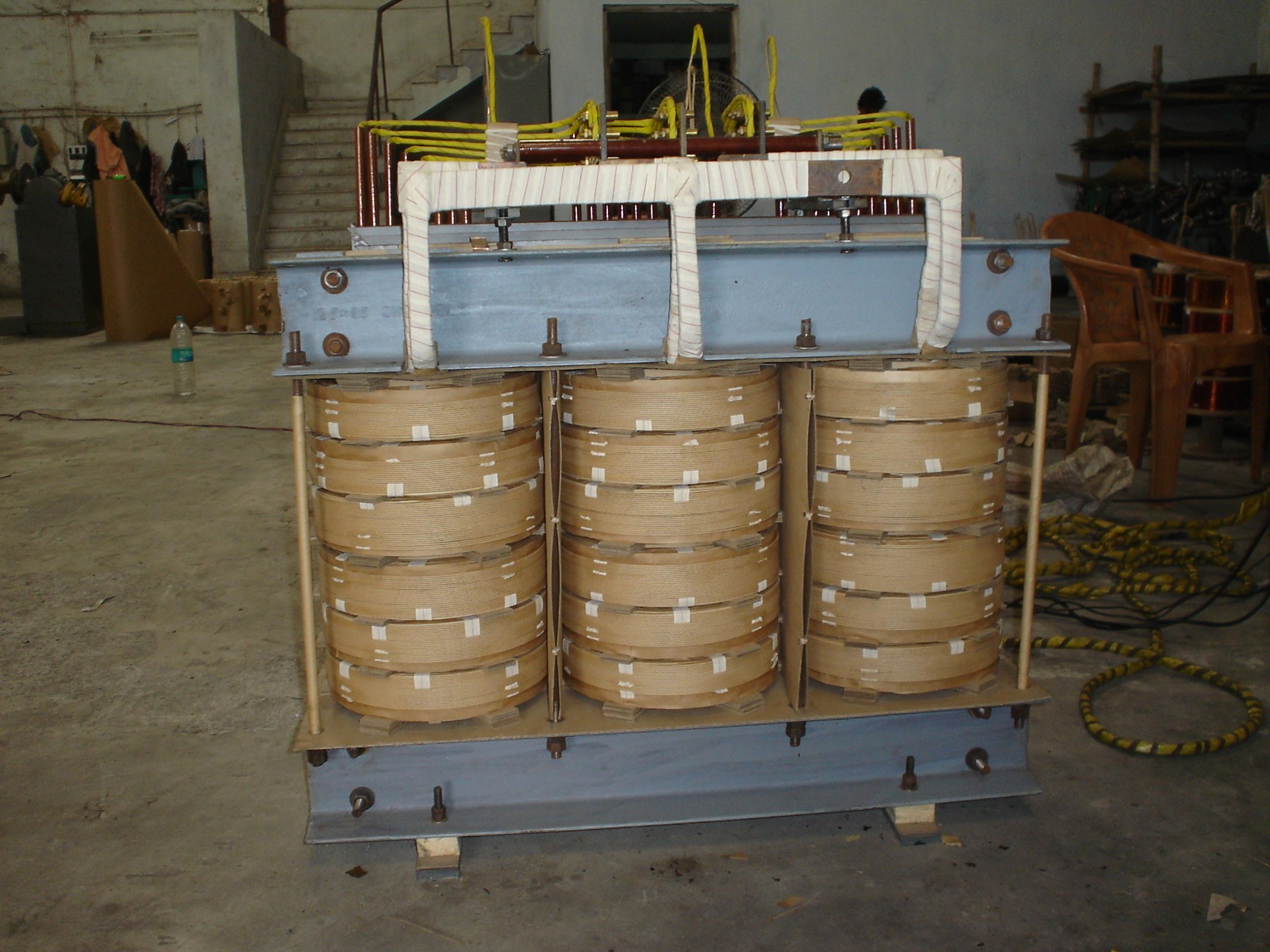
CORE COIL ASSEMBLEY
The assembled Core and H.V and L.V Coils are now taken up for Core-Coil assembly. The core assembly is vertically placed with its foot touching the ground. The top yoke of the core is removed. The limbs of the core are tightly wrapped with cotton tape and then varnished. Cylinders made out of Insulating Press Boards is wrapped on all three limbs. L.V.Coils are placed on the insulated core limbs. Insulating block of specified thickness and number are placed both at the top and bottom of the L.V
TANK UP
The Tanks fabricated as per Drawings using Good Commercial Grade Low carbon Steel having thickness as required from our fabricators. The inside of the tank is painted with specified quality Heat Oil resistant paint and fittings like drain valve, HV & LV Bushings ,Oil level Indicator etc are fitted in the tank. The Core-Coil assembly is then placed in the tank and properly locked. Transformer Oil is filled to immerse only the coil assembly. All the connections of primary and secondary terminals a
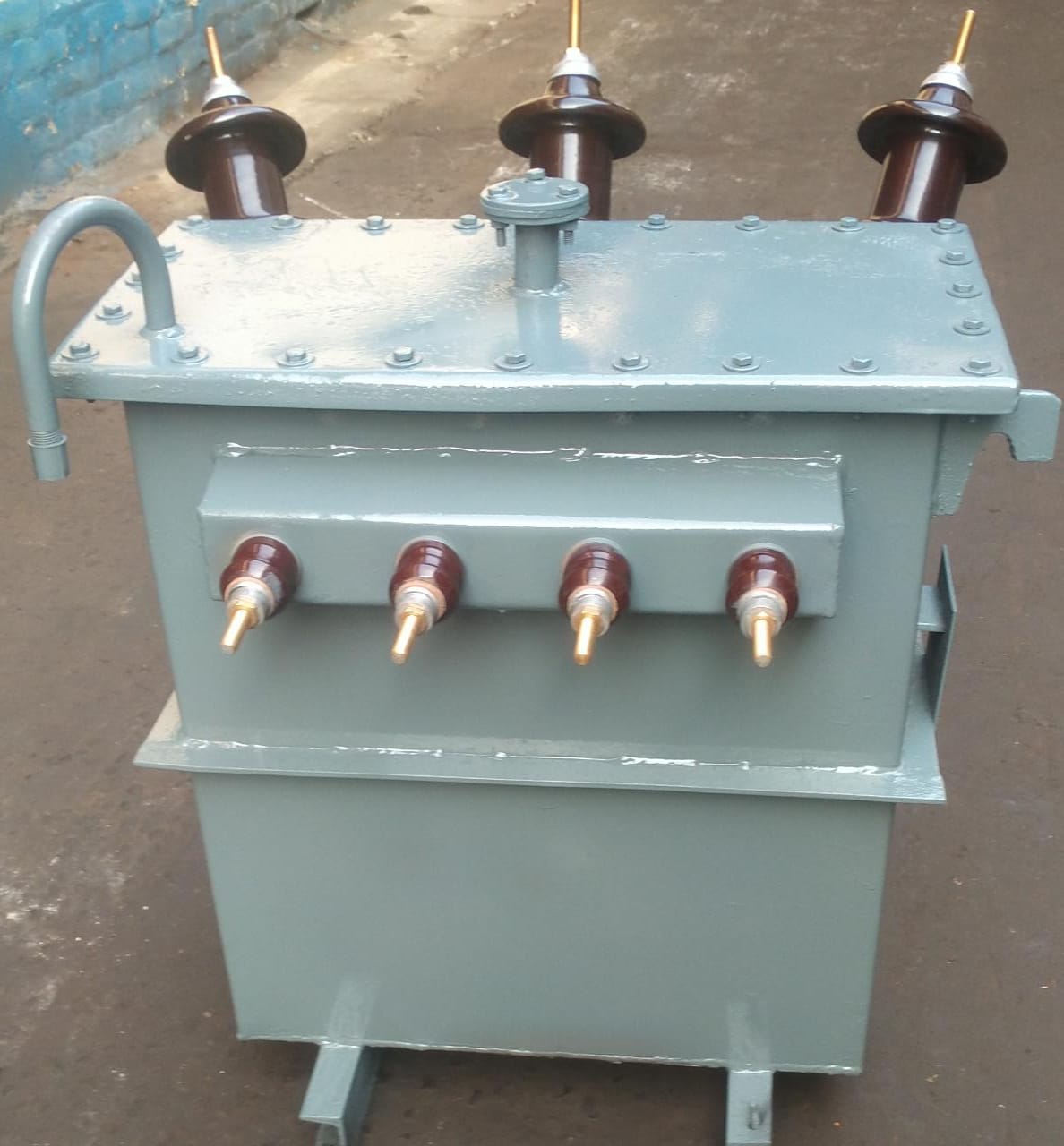
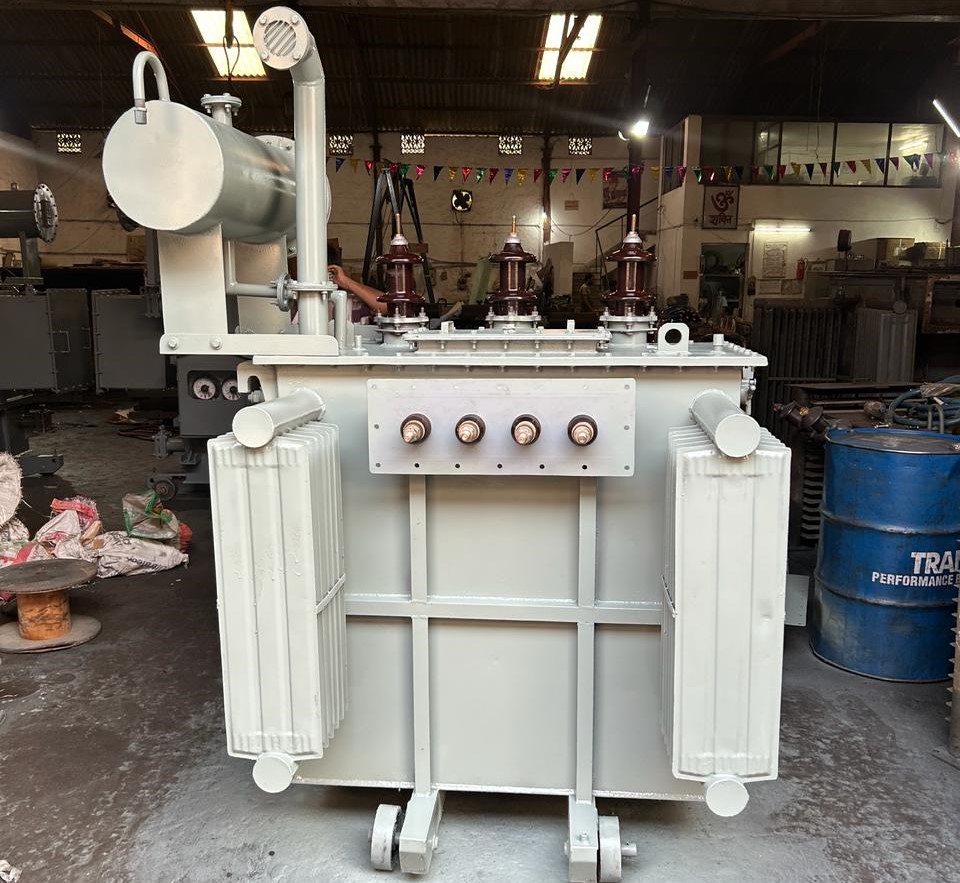
PAINTING AND FINISHING
The first step is proper cleaning of surface of the tank by chipping/grinding. After cleaning as per requirement One coat of primary paint of Zinc Chromate followed by two coats of Paint is applied. Fittings & Accessories are checked as per customers requirement and the Completed Job Is now ROUTINE TESTED as per IS 1180 & 2026. Dry Type IS 11171